Direct Examination Results of High Strength Versus Low Strength Steels
The Dilemma Found During Investigative Digs
Abstract
Due to great chemistry and metallurgical innovations of the steel industry, higher strength steels have made significant strides, in specified minimum yield strength (SMYS), wall thickness control, toughness, weight per foot, etc. However, one significant factor in these great improvements was no consideration for corrosion allowances. It has decreased with every incremental increase in the making of higher strength steels. Corrosion in carbon steel is the same whether it is a 35,000 yield pipe or an 80,000-yield pipe or 0.375” wall thickness versus 0.215” wall thickness. 25% wall loss on 35,000 yield pipe results in a 44% on the higher strength steel pipe. Lower strength steel direct assessment results in recoat type repair while higher strength steel results in a composite repair or replacement. Unfortunately, the US coating industry and pipeline operators have not kept up with these changes to offset or complement the improvements in great improvements made in higher strength steel. The dilemma, either add more corrosion allowances to the steel and/or improve the coatings. Coatings are supposed to be the first line of defense against corrosion control while cathodic protection is secondary.
Introduction
Efforts have been made in the development of high strength steels that have made great strides to pipeline projects in cost reduction while increasing operating pressures. In addition, the use of high strength steels has made an impact in the reduction of wall thickness which resulted in less material, shipping and welding costs. These developments have improved the toughness properties of the steel as well as the ability of the weldability even under field and ambient conditions. This has resulted in the reduction of pipe construction costs especially with respect to shipping and reduced welding times for thinner wall thicknesses. Because it is difficult to prevent external corrosion on pipeline steels, controlling the corrosion rate through the use of coating and cathodic protection is the most economical solution. Increasing the wall thickness is another solution; however, it would negate or offset all the gain that were developed with high strength pipeline steels and associated costs.
Understanding the Problem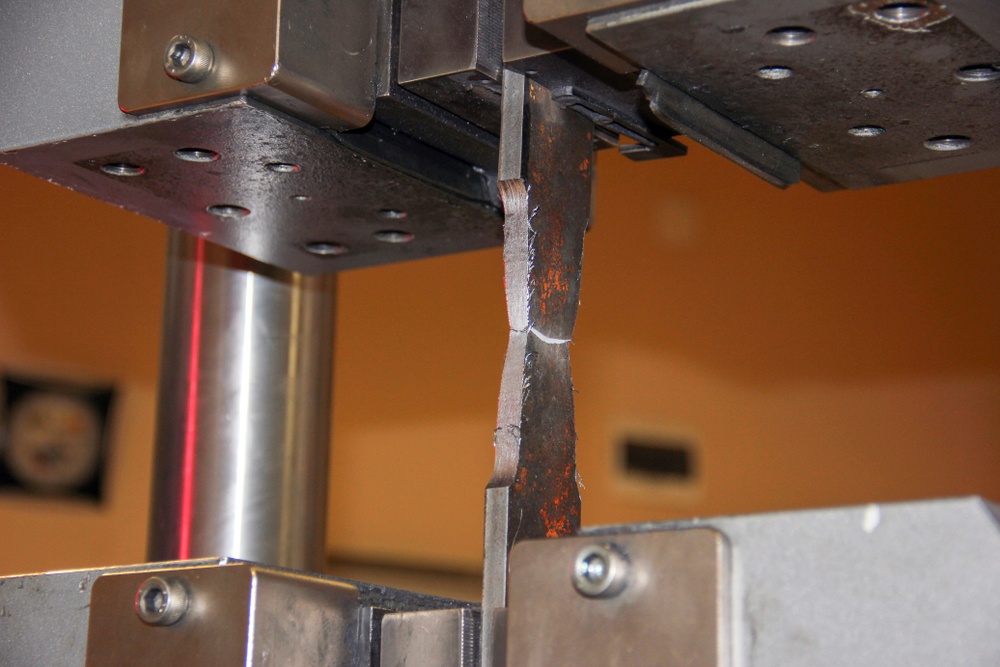
Because of the lack of extra or additional corrosion allowance from the older heavier wall pipe, we must better identify the mechanisms of corrosion and the methods of arresting corrosion process. There are many forms of corrosion; however, there are two primary methods of slowing the process down to a manageable/safe level to meeting industry standards and regulatory requirements. Coatings and cathodic protection (CP) work well for underground or submerged pipeline systems. The following is an overview of coatings and CP:
- Coatings are the first line of defense against external corrosion.
- Coatings are not perfect and must be cathodically protected to slow down the corrosion rate at breaks (holidays).
- Cathodic protection is applied to underground and submerged structures to prevent corrosion of the steel substrate at holidays.
- Coatings such as Fusion Bonded Epoxies (FBE) allow CP through micro-pores
- 14 to 16 mils coating thickness is common for line pipe
- 20 to 24 mils coating thickness is common for horizontal directionally drilled (HDD) crossings
- Types of coatings play an important role in the cathodic protection of the pipeline
- CP is used protect only the exposed metal substrate at small holidays.
- Smaller holidays reduce the size and high expense of operating cathodic protection systems.
- A well designed coated structure will ensure good current attenuation with cathodic protection.
There are many physical and chemical properties required for a good line pipe coating according to NACE. They are as follows:
- An effective electrical insulator
- An effective moisture barrier
- Can be applied to the pipe by a method that does not adversely affect the properties of the pipe
- Can be applied to piping with a minimum of coating defects
- Good adhesion to pipe surface
- Ability to resist development of holidays with time
- Ability to resist damage during handling, storage, and installation
In addition, NACE has many other considerations that are too numerous to mention for a good coating; however, many of the selection of properties are up to the pipeline operator and coating manufacturer and plant to put into their specifications. These physical and chemical properties are difficult to achieve such as how effective is effective and what is meant by resisting development of holidays.
Since the US, Canada and South America are the biggest users of Fusion Bonded Epoxy coatings for underground pipelines, industry has done little to demand that coating manufacturers address the appropriate changes as the wall thickness (WT) of the pipe were reduced. Corrosion rates on pipeline steels are the generally the same whether it is 0.5 inch W.T. lower strength steel or 0.25 W.T. or higher strength steel. What this means is running a remaining strength of corroded pipe calculation (RSTRENG) on thinner wall pipe will show that the safe operating pressure will be reduced more significantly thus resulting in a more advanced repairs such as a composite sleeve versus just a recoat and backfill. Understanding corrosion rates, monitoring and assessment will be the next article of this series.
First Step
As a bare minimum coating thickness should provide more than 99% of the protective needs of a buried or submerged pipeline. The remaining less than 1% needs to come from cathodic protection. Coatings should be designed deteriorate at a slow rate over the life of the pipeline system under normal and abnormal operating conditions. However, this is rarely the case due to many external factors that are rarely considered in the design of the pipe. What are some of the factors that impact coating deterioration? AC and DC interference issues either from power lines, transit systems or other pipelines. Aggressive soils such as clays with low pH or low resistivity, rock conditions, microbial activity, high water tables, etc. It is usually an after the fact issue and left up to the corrosion engineer to protect the pipe with additional cathodic protection. This is another study in itself to attempt to slow down these external factors.
One example is AC corrosion interference i.e. where pipelines are buried in AC transmission corridors. There have been cases where newly constructed pipelines experienced leaks within 6 months of installation due to AC corrosion. While this may be somewhat an extreme case, it catches the pipeline operator off guard and then the real studies begin in how to mitigate just this one issue. The costs can run into millions of dollars; whereas, if these factors where planned into the design of the pipeline coating type and mitigation at the time of construction, these issues could have been minimized. Once the pipeline coating system integrity has been compromised, then performance and risk of failure moves up on the risk ranking and re-assessment intervals become shorter which means additional frequency in pigging and other surveys. A follow up article will be forthcoming on AC interference issues, study and mitigation.
Second Step
Now that one of the factors have been identified, what type of coating is required for the life of the pipeline. Is a single coat needed or what about a dual (abrasion resistant overcoat) or triple layer coating similar to what the Europeans use? What is the optimum coating required for this set of conditions?
Let’s discuss line pipe coating types that are available as the first defense against corrosion.
- Anti-corrosion coatings
- Types
- Single layer FBE coating for line pipe 14 to 16 mils
- Two layer FBE coating with abrasion resistant overcoat – 20 to 24 mils
- Three layer with epoxy primer, co-polymer adhesive followed by high density polyethylene – Up to 120 mils
- Performance of these coatings is based on:
- Cleanliness, anchor pattern, acid wash, thickness, number of layers and type, etc.
- Transportation is based on:
- Storage, handling, shipping, installation and final testing
- Types
Most US pipeline operators use the FBE single layer for line pipe and 2 layer for road and water crossings. Unfortunately, very few pipeline operators order three (3) layer coating systems in the USA. Our European counterparts use the 3-layer type most of the time. These coating systems come very close to being an ideal (near perfect) coating system for most factors that are encountered in the field. I was fortunate to work for a large transmission company in the 80’s that tried out some of the first three layer systems in the US. A 30” diameter line, 130 miles in length, installed 1987 required only 0.5 amps to cathodically protect it in very low resistivity type soils. It is my understanding even today that the cathodic protection current requirements have not changed since 1987 since it was initially installed. This demonstrates that little or no deterioration has occurred in 29 years. We as an industry would be hard pressed to say that about conventional coating systems performing that well.
Because of acceptance of conventional coating systems, pipeline operators spend millions of dollars on In-Line Inspection (ILI) verification digs and repairs each year to maintain the integrity of their pipelines from external corrosion, cracking, material defects and mechanical damage. Operators run thousands of RSTRENG calculations (see RSTRENG Next Page) to make ensure that the pipeline can operate as it was designed.
Example: Lower Strength Steel
A 20-inch diameter line, 0.500 WT, 35,000 Yield, Design factor 0.5 with an 800 psig established MAOP. However, the design pressure calculation is 874 psig. The RSTRENG maximum safe operating pressure based on the worst pitted area is 887 psig. In this case it passed and will require recoat and backfill.
Example of a Higher Strength Steel
A20-inch diameter, 0.25 WT, 70,000 Yield, Design factor 0.5 with 800 psig established 800 MAOP. However, the design pressure is 874 psig. The RSTRENG maximum safe operating pressure based on the worst pitted area is 451 psig. This case failed which require a repair sleeve or cut-out to meet code requirements.
These are examples of what pipeline operators must deal with on a day to day basis due to on-going corrosion due to aged coatings. Even though coatings are the primary player, cathodic protection should be used to protect the smaller coating holidays on new pipe. As coating age, they should not degrade catastrophically which has been the case.
What is the Next Step?
There are multiple issues to address coatings and steel corrosion allowances such as:
- Consideration for additional corrosion allowances:
- Pipelines in AC and multiple pipeline corridors
- HDD road and water crossings
- High consequence and
- Environmentally sensitive areas
- Consideration for multiple layer coating systems:
- Same factors as above
- Interference areas due to adjacent CP systems, DC rail and AC transmission
- Aggressive soils
- Coating disbondment with time and impact (construction, rock backfill, transportation, etc.)
- Long term performance
- Utilize CP for the smaller holidays and not protect large areas meant for coating
Many of these factors are not always taken into consideration in the design of a pipeline with a 3-layer coating system. Then the coatings and corrosion engineer are faced with trying to minimize the corrosion rates through CP rather than the use of protective coatings. However, these initial coating costs need to be weighed again continual maintenance, additional CP, shortened ILI re-assessment intervals, repairs, replacement and worst of unanticipated failures.
Summary
Coatings must be the first line of defense against corrosion. Selection and understanding of the physical and chemical properties must be known before selecting the type for long term performance. Cathodic protection should be the secondary factor, not the primary factor in protecting the pipe and related underground facilities. Too often the CP systems become the primary defense against corrosion once the line is commissioned. A small investment in multi-layer coating systems means better integrity management and lower maintenance costs down the road. Good coatings must minimize coating disbondment, reduce CP levels in the short as well as the long term while impact issues. Training and informing corrosion engineers, managers, procurement people must be a priority in our industry.