Hydrostatic Testing in Pipelines: Ensuring Structural Integrity
By Kesley Price
Introduction
Ensuring the structural integrity of pipelines is paramount for the safe and efficient transport of liquids and gases. Hydrostatic testing stands out as a critical technique in this endeavor. Hydrostatic testing is a crucial technique in this process. This blog will explore the principles of hydrostatic testing, its importance in maintaining structural integrity, and the standards and safety measures associated with this essential practice, referencing comprehensive technical resources to provide a detailed analysis.
The Principles of Hydrostatic Testing
Hydrostatic testing, or hydrotesting, involves filling a pipeline with water and pressurizing it to a level higher than its operational pressure. This process helps identify leaks, weaknesses, and ensure the overall integrity of the pipeline before it is put into service.
Key Principles:
- Filling the Pipeline: Water is chosen due to its incompressibility, ensuring even minute leaks can be detected. The process involves removing air pockets, as air can compress and lead to inaccurate results.
- Pressurizing the Pipeline: The pipeline is subjected to a pressure exceeding its normal operating conditions, typically 1.25 to 1.5 times the design pressure. This overpressure ensures that any weaknesses in the pipeline are exposed.
- Holding the Pressure: The pressure is maintained for a specified duration, usually 8 to 24 hours, to monitor for any pressure drops indicating leaks. Continuous monitoring is essential to detect even the smallest pressure changes.
- Depressurization and Inspection: After the test, the pressure is gradually reduced to prevent sudden changes that could damage the pipeline. A thorough inspection follows to identify any signs of deformation or failure.
Importance of Hydrostatic Testing
Hydrostatic testing is crucial for several reasons:
- Verification of Structural Integrity: It ensures the pipeline can withstand operational pressures without leaking or bursting.
- Detection of Defects: Even small leaks or material weaknesses can be identified, which might not be visible during regular inspections.
- Safety Assurance: By testing beyond normal operating conditions, hydrostatic tests help prevent potential catastrophic failures.
- Compliance with Standards: Regulatory bodies and industry standards mandate hydrostatic testing to ensure pipeline safety and reliability.
Standards and Regulations 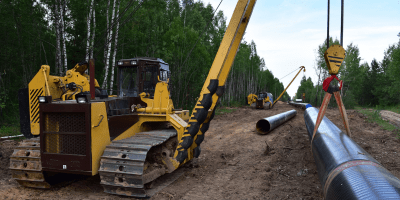
Adhering to established standards is vital for the effective implementation of hydrostatic testing. Some of the key standards include:
- ASME B31.8: Specifies the requirements for gas transmission and distribution piping systems, including hydrostatic testing procedures.
- API 1110: Provides guidelines for the pressure testing of liquid petroleum pipelines.
- ISO 13623: International standard for the design and operation of pipeline transportation systems.
Technical Aspects of Hydrostatic Testing
Hydrostatic testing involves a series of technical steps and considerations to ensure thorough testing and accurate results.
Pre-Test Preparation:
- Design Considerations: Determine test parameters, including maximum allowable operating pressure (MAOP) and test pressure. Factors such as pipeline material, diameter, and wall thickness influence these parameters.
- Pipeline Inspection: Assess the pipeline’s condition, ensuring all welds, joints, and fittings are secure and in good condition. Conducting a visual and ultrasonic inspection helps in detecting any pre-existing defects.
- Test Medium Selection: Water is commonly used due to its incompressibility, though other fluids may be used in specific scenarios. The water quality should be controlled to prevent corrosion and scaling inside the pipeline.
Analysis and Data Interpretation
Post-test analysis is critical for evaluating the pipeline’s integrity. Key aspects include:
- Pressure Data Analysis: Analyze pressure readings to identify any drops indicating leaks. Advanced data logging systems are often used to record pressure and temperature continuously during the test.
- Visual Inspection: Inspect the pipeline for visible signs of damage or deformation. This inspection is typically done using both internal and external methods, including in-line inspection tools.
- Documentation: Record all test parameters, pressure data, and inspection results for compliance and future reference. Proper documentation is essential for regulatory compliance and future maintenance planning.
Hydrotest Safety Measures
Hydrostatic testing involves high-pressure systems, making safety measures paramount. Key safety precautions include:
- Proper Training: Ensuring personnel are adequately trained in hydrostatic testing procedures and safety protocols. This includes understanding the test setup, potential hazards, and emergency procedures.
- Equipment Checks: Regular inspection and maintenance of testing equipment to prevent failures during the test. This includes verifying the calibration of pressure gauges and ensuring the integrity of hoses and fittings.
- Monitoring and Communication: Continuous monitoring of pressure levels and clear communication among the testing team. Establishing a clear line of communication helps in quickly addressing any issues that arise during the test.
- Emergency Preparedness: Having an emergency response plan in place in case of any unexpected incidents. This plan should include procedures for dealing with sudden pressure releases, equipment failures, and personnel injuries.
How Technical Toolboxes and the Hydrotest PowerTool Assist in Hydrostatic Testing
Technical Toolboxes provides a suite of tools and resources designed to enhance the hydrostatic testing process. The Hydrotest PowerTool, in particular, is an invaluable resource for engineers and technicians involved in pipeline integrity verification.
Benefits of the Hydrotest PowerTool:
- Streamlined Planning: The Hydrotest PowerTool aids in the meticulous planning of hydrostatic tests by providing detailed guidelines and best practices. It ensures that all necessary parameters are considered, including test pressure, duration, and environmental conditions.
- Data Management: This tool offers advanced data logging and management capabilities, allowing for the continuous recording of pressure, temperature, and other critical parameters. This data is essential for post-test analysis and regulatory compliance.
- Comprehensive Reporting: The tool generates detailed reports that document every aspect of the test, from initial setup to final inspection. These reports are crucial for audit trails and ensuring compliance with industry standards.
- Safety Enhancements: The Hydrotest PowerTool integrates safety protocols and checklists to ensure that all safety measures are strictly followed during the testing process. This reduces the risk of accidents and enhances overall test reliability.
Conclusion
Hydrostatic testing is a vital procedure for ensuring the structural integrity of pipelines. By adhering to established standards and implementing rigorous testing protocols, the safety and reliability of pipeline systems can be significantly enhanced. Technical Toolboxes and the Hydrotest PowerTool provide the necessary tools and support to conduct efficient and reliable hydrostatic tests, ensuring that pipelines meet all safety and integrity requirements. This practice helps detect potential issues before they become critical and ensures compliance with industry regulations, ultimately safeguarding the environment and public safety.
Suggested Post
The API Inspector’s Digital Revolution
The API Inspector’s Digital Revolution: Maximize Field Time, Cut Report Delays, and Prove Return [...]
Intro to AI in Midstream: What’s Here, What’s Next, and What Still Needs You
Intro to AI in Midstream: What’s Here, What’s Next, and What Still Needs [...]
Horizontal Directional Drilling (HDD): Designing for Success
Horizontal Directional Drilling (HDD): Designing for Success By David Willoughby Minimize Risk and Optimize [...]