The Essential Role of API 510 and 570 Inspections in Asset Integrity
By Kesley Price
Understanding API 510 and 570 Inspections
API 510 and 570 are key standards issued by the American Petroleum Institute (API) that govern the inspection, repair, alteration, and rerating of in-service pressure vessels (API 510) and piping systems (API 570). These standards are crucial for maintaining the safety and integrity of these essential components in the oil and gas midstream and downstream industries, as well as chemical industries.
API 510: Pressure Vessel Inspection Code
API 510 covers the in-service inspection and integrity assessment of pressure vessels. It provides guidelines on maintaining the pressure vessels’ mechanical integrity throughout their operational life. Inspections under this code help identify areas susceptible to corrosion, fatigue, or other degradation processes that might compromise the vessel’s safety.
API 570: Piping Inspection Code
Similarly, API 570 applies to in-service piping systems, offering standards for inspection, repair, alteration, and rerating. It focuses on ensuring the piping systems are safe, reliable, and capable of continued operation. This code helps facilities avoid leaks, bursts, and other failures that can lead to environmental damage, financial loss, or even catastrophic accidents.
The Inspection Process 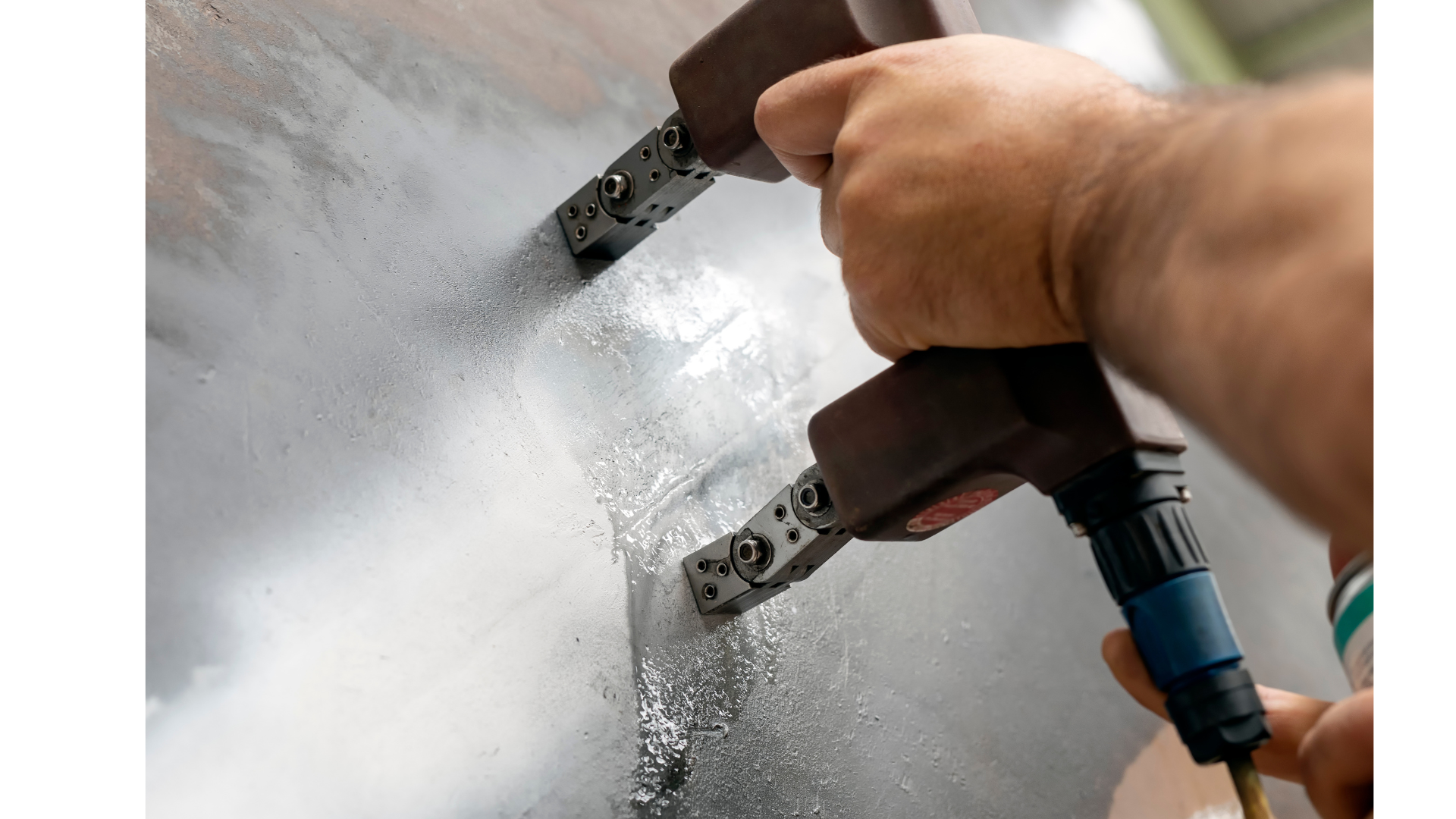
The inspection processes for both API 510 and API 570 involve several key steps:
- External Inspection: Visual checks to identify surface deterioration, deformations, and external leaks
- Internal Inspection: Detailed checks when a vessel or system is out of service, focusing on internal components for signs of wear or corrosion
- Thickness Measurements: Regular measurements to monitor thinning due to corrosion or erosion
- Non-destructive Testing (NDT): Techniques like ultrasonic testing and radiography to detect subsurface flaws
How Software Can Streamline API Inspections
Leveraging software solutions in API inspections can vastly improve the efficiency and accuracy of these processes. Here’s how software can help API Inspectors:
Data Management and Reporting
Software tools designed for API inspections can handle vast amounts of data from various sources, making it easier to track the history and condition of vessels and piping systems. Software enables seamless reporting and documentation, which is crucial for API compliance and historical records.
Automated Calculations
These tools often include features for automated calculations that can predict degradation rates and remaining life estimates. This not only speeds up the inspection process but also enhances its accuracy, helping plant managers make informed decisions about maintenance and operations.
Integration with Other Systems
Integration capabilities with GIS systems, Asset Management, and other operational platforms allow for a holistic view of the plant’s operations. This integration helps in planning maintenance activities more effectively and ensures that all parts of the plant are regularly monitored and maintained.
Conclusion
API 510 and 570 inspections are indispensable for ensuring the safety and efficiency of industrial operations involving pressure vessels and piping systems. The implementation of dedicated software tools not only simplifies these inspections but also enhances decision-making, ensuring that assets remain in optimal condition throughout their operational lifecycle. Adopting these practices is not just about compliance; it’s about ensuring the safety of operations and the protection of both human lives and the environment.
Learn more about Technical Toolboxes’ API Toolbox.
Suggested Post
The API Inspector’s Digital Revolution
The API Inspector’s Digital Revolution: Maximize Field Time, Cut Report Delays, and Prove Return [...]
Intro to AI in Midstream: What’s Here, What’s Next, and What Still Needs You
Intro to AI in Midstream: What’s Here, What’s Next, and What Still Needs [...]
Horizontal Directional Drilling (HDD): Designing for Success
Horizontal Directional Drilling (HDD): Designing for Success By David Willoughby Minimize Risk and Optimize [...]