The Role of B31G in Pipeline Integrity Assessments
By Kesley Price
Pipeline integrity is crucial for ensuring the safe and efficient transportation of oil, gas, and other substances through pipeline networks. Among the various methods used for pipeline integrity assessments, the ASME B31G standard plays a pivotal role, especially in evaluating corrosion defects.
What is B31G?
B31G is a method used to evaluate the remaining strength of pipelines affected by corrosion. Originally developed by the American Society of Mechanical Engineers (ASME), it helps pipeline operators determine if a corroded section of the pipe is still fit for service. B31G, in both its original and modified versions, offers a simplified approach to assess whether repairs are needed and what operational pressures the pipe can safely handle.
Key Role in Corrosion Defect Analysis
Corrosion is one of the primary threats to pipeline integrity. Over time, external and internal factors can degrade the pipe’s wall, reducing its thickness and structural integrity. The B31G method simplifies this complex issue by providing a calculation that estimates the maximum allowable operating pressure (MAOP) of a corroded pipeline. This is achieved through a comparison between the pipe’s original thickness and its current state after corrosion.
By using B31G, operators can decide whether a pipe section needs immediate repair or if it can remain in operation for a certain period without compromising safety.
B31G’s Evaluation Process 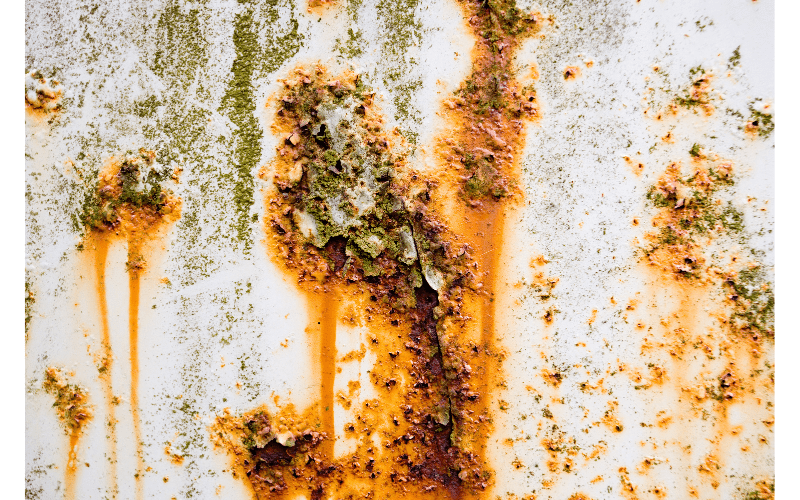
The B31G method relies on measuring the dimensions of a corrosion defect, such as its length, depth, and width, as well as knowing the pipe’s material properties. The process involves:
- Estimating Remaining Strength: Based on the measured defect dimensions, B31G calculates the failure pressure. This pressure is then compared to the pipeline’s operational conditions.
- Modified B31G: An improvement to the original formula, offering a more conservative estimation of failure pressure, especially for larger and more complex corrosion areas. This provides operators with more reliable data to prevent failure.
RSTRENG: A Complementary Tool
While B31G provides essential guidance, the RSTRENG method (Remaining Strength of Corroded Pipelines) offers a more detailed evaluation. RSTRENG uses an effective area calculation to provide more precise results, especially for complex corrosion profiles that B31G might oversimplify. Tools like the RSTRENG+ software enhance this process by automating calculations and integrating them into pipeline management systems.
Importance in Pipeline Repair Strategies
B31G serves as a vital decision-making tool for pipeline repair strategies. By providing a clear understanding of a pipe’s capacity, operators can:
- Prioritize Repairs: Allocate resources to the most critical areas, focusing on defects that pose the highest risk of failure.
- Extend Pipeline Life: B31G helps operators safely extend the operational life of pipelines by identifying areas that are still fit for service, thus delaying expensive repairs.
- Minimize Downtime: With an accurate assessment of pipeline strength, operators can avoid unnecessary shutdowns and maintain optimal operational efficiency.
Compliance with Industry Standards
The B31G method aligns with federal and industry standards, including PHMSA’s regulations. It is widely accepted as a reliable approach to ensure pipeline safety in the face of corrosion. Furthermore, with advancements in software like Technical Toolboxes’ Pipeline Toolbox and RSTRENG+, operators can now seamlessly integrate these calculations into broader integrity management systems, ensuring compliance with federal standards like CFR 192 and 195.
Conclusion
The ASME B31G standard remains a cornerstone in pipeline integrity assessments. It simplifies the complex challenge of evaluating corrosion defects and informs critical decisions about pipeline safety and maintenance. Combined with tools like RSTRENG, operators can achieve greater accuracy, reduce risks, and prolong the service life of their pipeline assets, ensuring both safety and operational efficiency.
Suggested Post
The API Inspector’s Digital Revolution
The API Inspector’s Digital Revolution: Maximize Field Time, Cut Report Delays, and Prove Return [...]
Intro to AI in Midstream: What’s Here, What’s Next, and What Still Needs You
Intro to AI in Midstream: What’s Here, What’s Next, and What Still Needs [...]
Horizontal Directional Drilling (HDD): Designing for Success
Horizontal Directional Drilling (HDD): Designing for Success By David Willoughby Minimize Risk and Optimize [...]