Deciphering the Differences: MAOP and MAWP in Pipeline Operations
By Bryant Jerome
In the complex world of pipeline engineering, understanding, and managing operational pressure limits is essential to ensuring safety and reliability. Maximum Allowable Operating Pressure (MAOP) and Maximum Allowable Working Pressure (MAWP) are two fundamental metrics that engineers often use to describe the pressure limits a pipeline can operate under. Despite their similarity, these terms serve distinct functions and are based on different regulatory standards and design considerations. Here, we’ll break down the differences between MAOP and MAWP and explore their implications in pipeline operations.
Understanding MAOP and MAWP
MAOP refers to the maximum pressure at which a pipeline system is authorized to operate under normal conditions. Set by regulatory bodies, this limit is determined through a combination of engineering calculations, pipe properties (such as outer diameter or wall thickness), historical data, and field-testing results (e.g., hydrostatic testing). In the U.S., MAOP is regulated by standards such as 49 CFR Parts 192 and 195, and ASME B31.4 and B31.8. MAOP is calculated for pipeline segments to prevent excessive pressure, considering potential stress on materials, corrosion, and fatigue.
On the other hand, MAWP is the highest pressure that a single component or system can withstand before yielding or failing. This value is determined by the design of the weakest component, such as valves, fittings, or any segment of the pipeline system. Typically, MAWP takes into account the material strength, design factors, temperature, and wall thickness, adhering to codes like ASME Section VIII for pressure vessels.
Often there is a confusion between MAWP and Design pressure. MAWP is the highest level of pressure a component could be exposed to; the design pressure on the other hand is the highest level of pressure it should be exposed to in normal operating conditions.
Key Differences Between MAOP and MAWP
1. Calculation Basis:
-
- MAOP is calculated based on pipeline operational history and safety margins, often verified through hydrostatic tests that simulate maximum operating pressures under controlled conditions.
- MAWP is derived from the physical and structural limits of pipeline components, calculated without the operational safety factors that MAOP considers.
2. Purpose and Application:
-
- MAOP is focused on maintaining safe and continuous operations and is typically used in contexts involving long-distance transmission pipelines.
- MAWP is more about the integrity of individual pipeline components under extreme conditions, such as storage tanks and certain processing units, which may experience occasional surges or variations in pressure.
3. Regulatory Standards:
-
- For MAOP, pipeline operators must adhere to stringent guidelines set forth by federal agencies, such as the Pipeline and Hazardous Materials Safety Administration (PHMSA) in the U.S. MAOP regulations enforce routine assessments and recalculations to ensure ongoing pipeline integrity and safety compliance.
- MAWP falls under pressure vessel codes and standards such as ASME, with a focus on ensuring each component withstands its design pressure.
Safety Implications of MAOP and MAWP 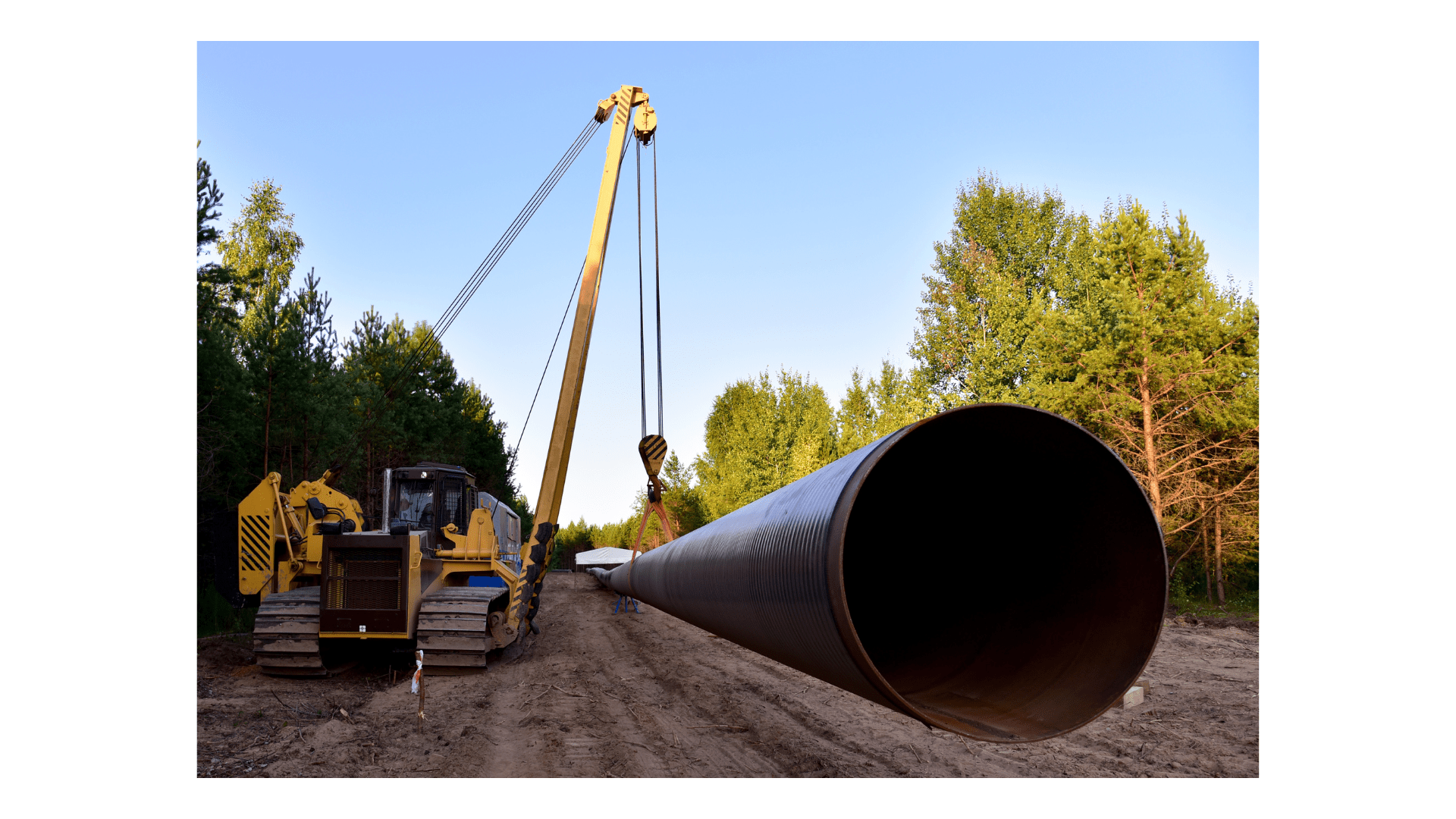
The distinction between MAOP and MAWP is not merely academic; it has serious safety implications in pipeline operations. Exceeding the MAOP can lead to leaks, ruptures, or catastrophic failures, posing threats to both the environment and public safety. As such, many operators utilize Technical Toolboxes’ Hydrotest PowerTool to validate and recertify MAOP for existing pipelines, ensuring that pressure limits remain compliant with safety standards.
Conversely, MAWP breaches typically signal a need for component replacement or redesign, as exceeding this limit compromises the structure’s integrity. Engineers must pay close attention to MAWP in areas where pipelines may interface with equipment that handles fluctuating pressures, like pumping stations or valve assemblies.
Operational Design Considerations
From a design perspective, both MAOP and MAWP must align with the intended use and operational environment of the pipeline system. Factors influencing these pressure limits and how they change over time include material selection, environmental conditions, corrosion mitigation, and compliance with codes like ASME B31.8 and API standards.
Technical Toolboxes’ Advanced Calculations tools provide engineers with critical functionalities to analyze how changes in pipeline design and environment influence MAOP and MAWP, through stress analysis, corrosion impact assessments, and batch scenario simulations designed to optimize these parameters. This allows engineers to determine optimal design pressure ratings with ease, accommodating both MAOP and MAWP requirements effectively.
Regulatory and Compliance Aspects
Both MAOP and MAWP are subject to regular audits and testing. Tools like Technical Toolboxes’ Pipeline Toolbox (PLTB) help streamline compliance by automating regulatory checks and storing essential asset data for ongoing MAOP and MAWP verification. Features like automatic reporting and record-keeping simplify the documentation process, ensuring that every pipeline segment meets federal standards for pressure management.
Conclusion
MAOP and MAWP, while similar in their pressure-related functions, serve distinct roles in pipeline operations. MAOP focuses on the safe operational pressure for pipelines, whereas MAWP is concerned with the structural limits of individual components. Both are essential in maintaining pipeline integrity and preventing failures that could lead to environmental and operational hazards. By leveraging the advanced tools offered by Technical Toolboxes, operators can confidently manage these critical pressure limits, ensuring safety and compliance in their ongoing operations.
Suggested Post
The API Inspector’s Digital Revolution
The API Inspector’s Digital Revolution: Maximize Field Time, Cut Report Delays, and Prove Return [...]
Intro to AI in Midstream: What’s Here, What’s Next, and What Still Needs You
Intro to AI in Midstream: What’s Here, What’s Next, and What Still Needs [...]
Horizontal Directional Drilling (HDD): Designing for Success
Horizontal Directional Drilling (HDD): Designing for Success By David Willoughby Minimize Risk and Optimize [...]