HDD Surface Area Consideration
By David Willoughby
There are many factors to consider when evaluating the technical feasibility of a Horizontal Directional Drilling (HDD) project. The first step is usually to conduct a site survey which is important for all HDD projects and is a significant part of the HDD site characterization. The site survey should include both surface and some level of subsurface investigations. Successful trenchless projects are usually based on a design that is specifically tailored to the site and the anticipated subsurface conditions. A primary consideration is the suitability of the project site for the layout of the required HDD equipment and the product pipe.
Site Factors for Consideration
Main site factors that impact the surface area’s feasibility for HDD include:
- Drill rig layout area
- Product cable or pipe layout area
- Required temporary and/or permanent easements
- Existing utilities
- Existing infrastructures such as railroads, highways, etc.
- Adjacent property and any use restrictions
- Future developments in the area
The surface impact associated with the construction of a pipeline crossing by HDD is significantly less than the impact associated with construction by open-cut excavation. However, the HDD construction is not without some surface impact.
Entry and Exit Points for HDD Design
On many projects, the working areas for the entry and exit points must be cleared and graded to allow for HDD equipment and pipe pulling. When the work areas are limited, before declaring that an HDD project is not technically feasible, alternate scenarios for performing the HDD should be considered. One of the most crucial steps in HDD design is selecting the entry and exit sides for the crossing. For the driller, the entry, called the rig side, is where the drilling tool enters the ground. The other side is the pipe side or exit point. From a product pipe perspective, the term entry point is used for the pipe side. The entry pit collects mud returns from the hole and, if required, reduces the height of the catenary.
Typically, the pipe side is selected first because its requirements are more restrictive. However, there are also some requirements for the rig side related to available space, water supply, and access roads for the equipment and crew. Be sure that sufficient water is available during all critical phases of the job.
Positioning the Rig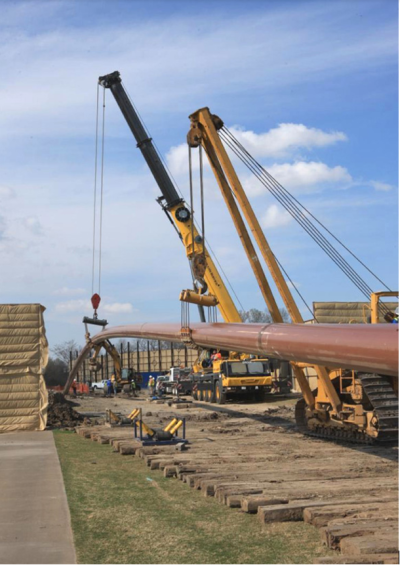
Space requirements will vary depending on the make and model of the drilling rig and how the various components may be positioned. However, the location of the principal components of the rig is fixed by the entry point. The rig ramp must be positioned in line with the drilled segment and approximately 25 feet back from the entry point. The control van and pipe must be positioned adjacent to the rig and the workspace must be cleared and graded level.
The equipment is typically supported on the ground surface, at times with timber mats where soft ground is encountered. For marine locations, it is possible to operate from barges.
The most important requirement for the pipe side is space for the pipe string. The location of pull section fabrication workspace is controlled by the drilled segment exit point. Space must be available to allow the pipe to be fed into the drilled hole. It is preferable to have a workspace in line with the drilled segment and extending back from the exit point the length of the pull section plus 200 feet. This will allow the pull section to be prefabricated in one continuous length prior to installation. If space is not available, the pull section may be fabricated in two or more sections that are welded together during installation.
However, the risk of getting stuck during a pullback is increased when having to tie-in in two sections. A tie-in may last hours because the pipe must be aligned, welded, and allowed to cool down before x-ray inspection; and the joint must be coated and allowed to dry (if necessary).
Using an HDD Design Tool for Validation
Technical Toolboxes Horizontal Directional Drilling PowerTool (HDDPT) provides a comprehensive solution to guide in the design validation, engineering, and installation phases of horizontal drilling. With HDDPT, the drilling efficiency and borehole stability can be maximized by identifying fluid characteristics and mud requirements, minimizing unnecessary costs and risks. Using advanced industry knowledge, HDDPT allows for complex borehole design, multi-section horizontal and vertical bends, and variable entrance/exit points while also performing pull force and installation stress analyses for both polyethylene and steel pipes. HDDPT is not only designed to support both gas and liquid pipelines; it can also support the calculations for installing cables and conduits as well.
More on HDD
For more information regarding this blog topic, read our Product Pipelines Stress During HDD or join me in our HDD for Pipelines – Engineering Applications for Feasibility, Design and Stress Analysis (2-DAY) Training.
training. You can also contact me, the author, David Willoughby, at [email protected]
Suggested Post
The API Inspector’s Digital Revolution
The API Inspector’s Digital Revolution: Maximize Field Time, Cut Report Delays, and Prove Return [...]
Intro to AI in Midstream: What’s Here, What’s Next, and What Still Needs You
 Intro to AI in Midstream: What’s Here, What’s Next, and What Still Needs [...]
Horizontal Directional Drilling (HDD): Designing for Success
Horizontal Directional Drilling (HDD): Designing for Success By David Willoughby Minimize Risk and Optimize [...]