Preserving the integrity of In-Service Welding
By Amirali Panjwani
Introduction
Pipeline engineers and operators utilize Hot-Tap or In-service welding techniques to connect and redirect live oil and gas pipelines without the need for expensive shutdowns. They encounter various challenges that require them to find a delicate balance between operational efficiency, safety considerations, and cost management.
Considerations When Selecting a Thermal Analysis Software
With the range of options available today, it can be challenging to determine the varying levels of value offered by each option. The following are some key factors to take into consideration when making a selection:
Operational Safety
Pipelines are susceptible to hydrogen cracking due to cooling too quickly after the welding process as contents that are flowing through remove heat quickly. Higher levels of heat are required to avoid this while ensuring, at the same time, that the welding torch does not burn through the pipe itself. Executing Hot-Tap welding properly from the beginning minimizes potential risks in the HAZ down the line. Software solutions provide significant value by ensuring that the operation remains within the safety parameters, effectively preventing issues such as burn-through and hydrogen cracking.
Industry Standards
Safety is a fundamental aspect of pipeline welding and is governed by explicit standards outlined in a range of rules and guidelines. These regulations ensure the safety of personnel and the integrity of the pipeline system. To adhere to these standards effectively, software solutions play a crucial role by supporting and facilitating compliance. These solutions help streamline processes, monitor safety parameters, and provide safeguards that all welding activities are conducted in accordance with the prescribed guideline, mitigating potential risks and promoting a safe working environment.
Managing Cost
When conducted safely, the cost of Hot-Tapping proves advantageous compared to alternatives that involve interrupting product flow during repairs or branch connecting operations. Success in the oil and gas industry necessitates the utilization of tools that enable safety analysis and prevent expensive maintenance shutdowns. Software solutions are essential in managing such risks and preventing excessive operational and capital expenditures. By leveraging software solutions, companies can strike a balance between risk and cost, ensuring efficient and safe pipeline operations while minimizing financial disruptions.
While weighing these key factors and challenges, the question often arises, should the solution be built, or should it be bought? The answer lies in probing the following elements:
Building a Hot-Tap Analysis Solution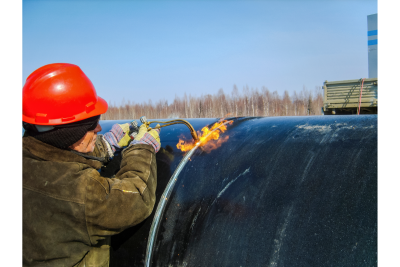
In most cases, building a Hot-Tap analysis is carried out through the use of spreadsheets. This method of analysis can pose many obstacles for the user as but not limited to the:
- Knowledge Transfer: When a solution is built manually, usually by an engineer, the methods, formulas, and calculations are put at risk when the solution’s creator either leaves or retires. The knowledge of the solution may not properly be handed over to the successor and this can result in increased expenditure.
- Limitations: Having to sift through multitudes of data along with a lack of integration and difficult reporting capabilities can make for a tedious process that can be excessively time consuming.
- Reliability: Spreadsheets are prone to human error, lack control and security, and can be difficult to troubleshoot or test, among other things. These issues can lead to an unsecure solution that may put the operation at a greater risk rather than solving the problem.
Buying a Hot-Tap Analysis Solution
Buying a software solution can oftentimes relieve the challenges posed by spreadsheets while providing additional benefits:
- Ease-of-use: A ready-made software solution will usually provide an intuitive UI, automation, and integration capabilities allowing the pipeline engineer to focus on the task at hand rather than worrying about the software they are using.
- Documentation: With automated reports and integration, pipeline engineers and organizations as a whole can comply with requirements for traceable, verifiable, complete (TVC) recordkeeping.
- Customer Support: Troubleshooting is made easier with experts available to aid in issues that arise with the software and who can provide periodic updates to the software to improve faults and issues.
PRCI Thermal Analysis as a Solution
Technical Toolboxes PRCI Thermal Analysis Software is an industry trusted solution developed in partnership with PRCI for welding calculations and thermal analysis. This software is based on a complex finite element mathematical model using a proprietary finite-element solver developed at the Edison Welding Institute (EWI). Pipeline engineers can use this software for modeling heat input and predicting the cooling rate to avoid hydrogen cracking for a given weld location while the pipe is in-service. The Thermal Analysis Software provides an additional assessment of attachments (sleeves, branches, etc.) to the pipe along with heat sink capacity calculations that take microstructures of the pipe/attachments into account as well. It is compliant with industry standards and regulations including API 1104, API 1107, ASME Section IX, BS4515, BS6990, and CSA Z662.
The PRCI Thermal Analysis Software is the ideal solution to support calculations and business processes throughout the life of a pipe. It offers pipeline engineers and welders a predictive model which ensures reliable cooling rates and optimized heat sink capacities among other benefits to expedite project schedules and decrease the long-term expenses associated with essential pipeline assets. By utilizing this software, engineers and welders can enhance the reliability of their operations, resulting in improved efficiency and cost savings over time.
More Information
For more information regarding this blog topic, please join us for our training on “What you need to know about in-service welding“.
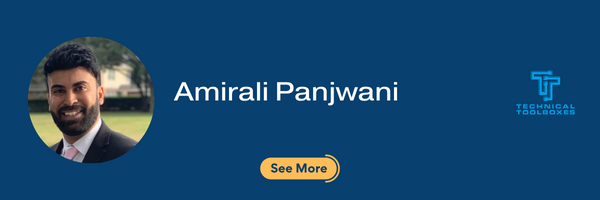
The API Inspector’s Digital Revolution
The API Inspector’s Digital Revolution: Maximize Field Time, Cut Report Delays, and Prove Return [...]
Intro to AI in Midstream: What’s Here, What’s Next, and What Still Needs You
 Intro to AI in Midstream: What’s Here, What’s Next, and What Still Needs [...]
Horizontal Directional Drilling (HDD): Designing for Success
Horizontal Directional Drilling (HDD): Designing for Success By David Willoughby Minimize Risk and Optimize [...]