The Misunderstood Significance of “Pre-1970” ERW
By Bill Amend
Figure 1 – Cross sections through examples of HF ERW (top) and LF ERW (bottom),
both showing no indication of the preferred normalized heat treatment condition.
Introduction
In discussions of the integrity characteristics of electric resistance welded (ERW) pipe there is sometimes undue emphasis put on pipe manufactured before 1970 versus pipe manufactured in 1970 or later. In reality, there is a wide range of details in manufacturing practices that existed simultaneously among the various pipe manufacturers as ERW pipe evolved from its beginnings in the late 1920s.
Historical Context
1970 is significant only because it is highly unlikely that line pipes manufactured after that date will be made using low frequency ERW (LF ERW) manufacturing practices. In the decade leading up to 1970, both LF ERW and high frequency ERW (HF ERW) were being made. Before 1960 all ERW pipes were produced using either DC ERW or LF ERW. Note that LF ERW is still included as an acceptable manufacturing method by the current editions of ASTM pipe standards and for PSL 1 pipe in the current edition of API 5L.
Why is HF ERW Generally Considered Better Than LF ERW?
HF ERW tends to have fewer manufacturing flaws than LF ERW, and in fact, “stitching” flaws at the seam fusion line are normally found only in LF ERW. Other flaws, including hook cracks, fusion line deficiencies, and geometric deficiencies like radial offset and excessive flash trim can be found in all variants of ERW, although modern mill inspection practices ensure that the frequency of those manufacturing flaws is often lower than in earlier vintage pipe.
Why the 1970 Date is an Incomplete Indicator of Seam Integrity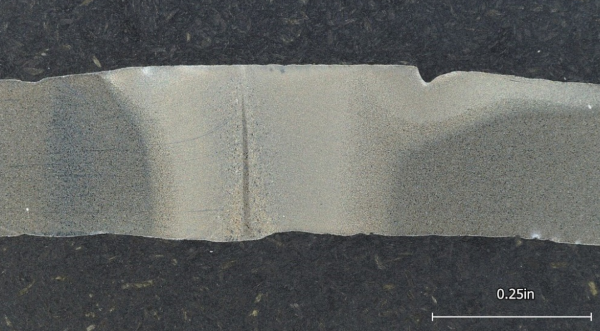
The often-overlooked consideration in ERW seam integrity management is that the long-term performance of ERW is related not only to the incidence of manufacturing imperfections but also to the metallurgical and mechanical properties of the seam. For example, selective seam corrosion (SSWC) is much more closely related to the steel composition and the type of seam heat treatment that was performed during manufacturing than to whether the seam was made by DC, LF, or HF variants of the ERW process.
Evolution of Heat Treatment Requirements
For many decades, no heat treatment of the seam was required by API 5L (or 5LX). Heat treatment requirements in the API pipe standards, summarized below, evolved over time, and actual heat treatment practices, as opposed to the minimum requirements of the API standard, also evolved and differed among the pipe manufacturers. Within the range of heat treatment options, a normalizing heat treatment, typically performed at temperatures of at least 1600°F, comes the closest to fully restoring the microstructure and properties of the seam to those of the base metal remote from the seam.
Heat Treatment Practices:
- No Heat Treatment: 5LX and 5L until 1966
- Tempering at 1000°F: 5LX 14th edition and 22nd edition of 5L (1967)
- Grades X42 and below (1995): Heat treat to eliminate untempered martensite
- Grades higher than X42 (1995): Normalize unless agreed upon
- Current Standards: PSL1: same as pre-41st edition, PSL2: all grades normalized unless otherwise agreed upon
Note that neither ASTM steel pipe nor API 5L PSL 1 ERW pipe has ever been required to receive a normalizing heat treatment.
Comparing Pre-1970 and Post-1970 ERW Pipe
Among the populations of either pre-1970 or later ERW pipe, there can be a wide range of ERW seam characteristics, depending upon the vintage, manufacturer, and the grade, since the final properties relate to the specific steels that were used and the heat treatment practices. Those seam characteristics translate to different susceptibilities to SSWC and to different abilities to tolerate seam imperfections without rupturing in service.
A Summary of ERW Seam Heat Treatment Requirements from API Specifications 5L and 5LX
Specification and Edition |
Heat Treatment Requirement |
5LX and 5L until 1966 | No heat treatment required |
5LX 14th edition and 22nd edition of 5L (1967) | 1000°F or elimination of untempered martensite |
5L 41st edition (1995): | Grades X42 and below: heat treat to eliminate untempered martensite
Grades higher than X42: normalize unless agreed upon |
5L 42nd edition (2000) to current | PSL1: same as pre-41st edition
PSL2: all grades normalized unless otherwise agreed upon |
More Information
For more information about variants of ERW pipe manufacturing practices and how they relate to the long-term integrity of the pipe seams, join us in the following webinars:
- Pipelines 101: An Introduction to the Pipeline Industry: August 8
- Pipeline Flaws and Degradation: August 15
- ERW Pipe: TBD
The API Inspector’s Digital Revolution
The API Inspector’s Digital Revolution: Maximize Field Time, Cut Report Delays, and Prove Return [...]
Intro to AI in Midstream: What’s Here, What’s Next, and What Still Needs You
Intro to AI in Midstream:What’s Here, What’s Next, and What Still Needs You By Marc Dungler AI [...]
Horizontal Directional Drilling (HDD): Designing for Success
Horizontal Directional Drilling (HDD): Designing for Success By David Willoughby Minimize Risk and Optimize [...]